Washington, IA – While politicians and pundits flocked to Iowa this winter in preparation for the presidential caucus, BRINC president John Brooks headed to the Hawkeye State with a very different purpose—bringing ThermalBuck to the fast-growing wall panel industry.
Washington, Iowa is home to the world’s oldest continuously running movie theater. It’s also home to Engineered Building Design (EBD), a panelized wall manufacturer serving clients from Minnesota to Texas. Their latest client, a developer of multi-family homes, wanted highly insulated walls using a combination of 2” Zip R-Sheathing and 2” ThermalBuck.
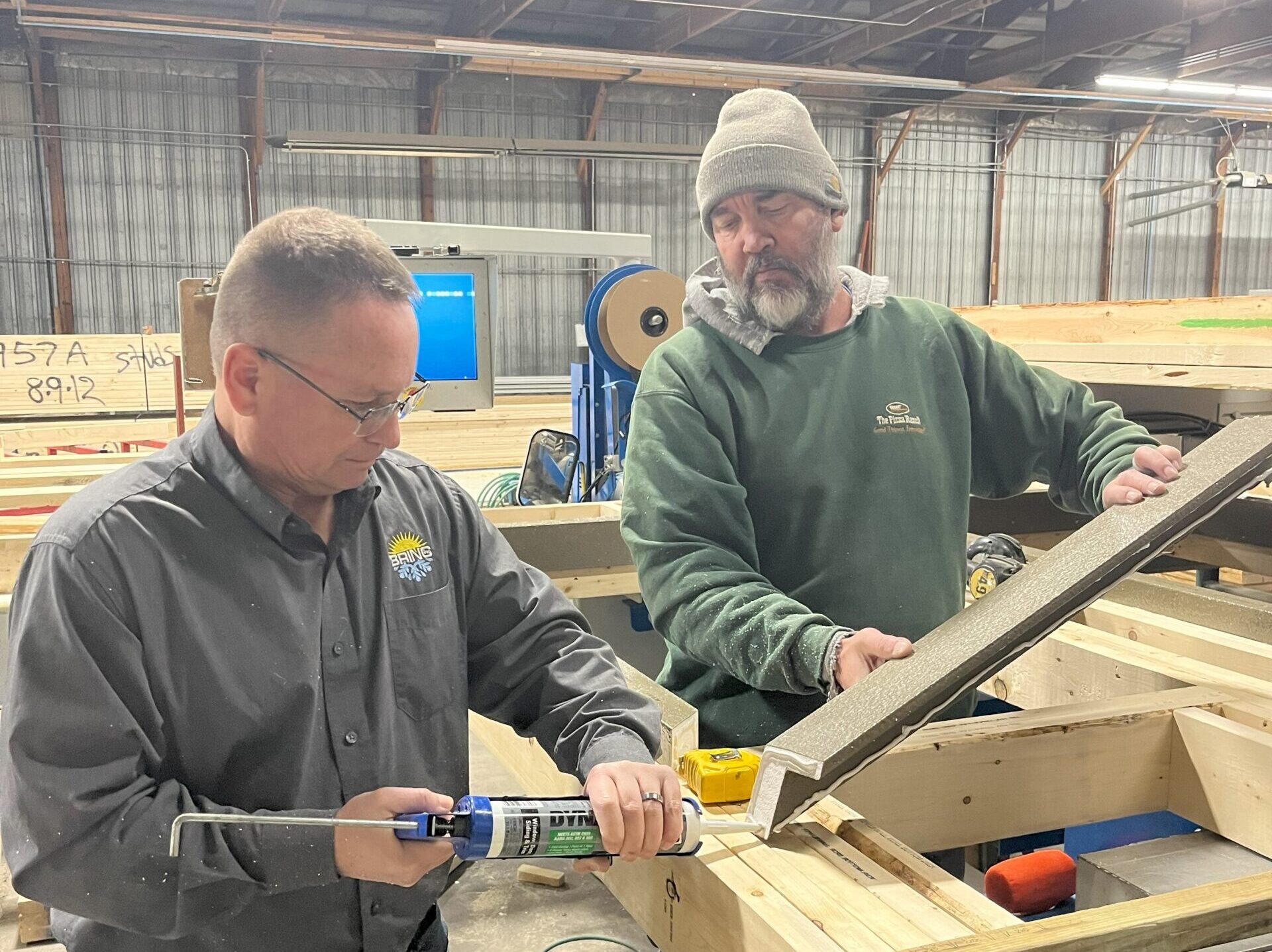
Panelized walls are known for high quality thanks to their production in a climate-controlled factory setting. Another plus is the consistency gained from assembly-line style construction.
Although they’ve used continuous insulation panels before, this was EBD’s first wall production using ThermalBuck. Because of this, John agreed to meet with the builders for a training installation. It was also an opportunity to learn about the emerging technology in wall plants like EBD’s.
“The combination of these two products is nothing new, but putting them together on a production line in a wall plant was new, at least for us,” John said.
Although wall prefabrication produces a consistent product quickly and efficiently, production requires the right amount of logistical expertise to nail down. Experienced builders must work in tandem to supply parts and pieces at the right time. In just the framing area, precut lumber came in from three different stations at once.
With rough openings for 5’x5’ windows and standard exterior doors, there was no shortage of learning opportunities for John or the framing team. The first challenge was deciding when to install ThermalBuck.
“After deliberation with their team, we decided to install ThermalBuck as the walls were being framed,” John explained.
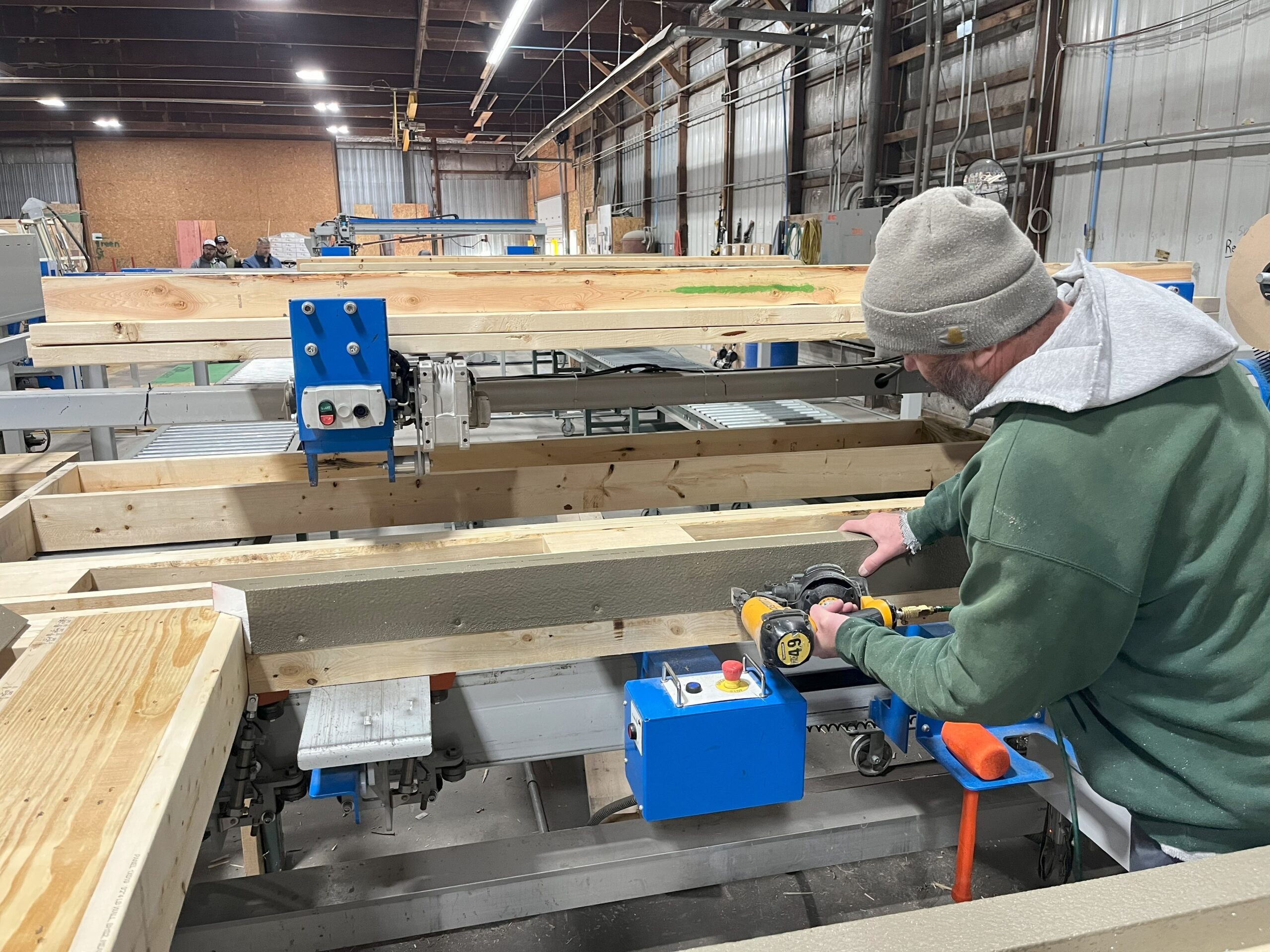
The R-Sheathing took more time to install thanks to special 4” nails required to fasten it. By installing ThermalBuck before the sheathing, there was additional time for preparation, including cutting and applying sealant.
“After a quick trial run, we realized that ThermalBuck could be precut just like the pieces of wood framing for the walls making this installation very fast,” John explained.
Donny, who operates the framing equipment, was open minded to the process and shared his honest feedback with us.
“The hardest part is you’ve got to know your angles and how to cut it,” Donny told us. “Installation is pretty simple. Just caulk your seams like they tell you. It’s a great product.”’
After installing ThermalBuck, the wall panel framing was completed, and the panel was sent down the line to have the R-Sheathing installed. Once complete, panels were checked for quality and stacked to await transportation to the site.
The bottom line—with some planning and preparation, ThermalBuck was integrated into the assembly line no disruptions or lost time.
For more information on Engineered Building Design and panelized wall manufacturing, visit ebdtruss.com.